Toll chemical manufacturing is an arrangement where a company manufactures or blends proprietary chemical products for other companies. The liquids and powders find uses in as-is finished products, food or drug nutrients, additives, coloring agents, catalysts, film coatings and special products for almost any industry.
These specialty chemical manufacturers are typically small- to medium-size plants that produce on slim profit margins in a competitive market. Their engineering and maintenance resources are stretched. The following shows how a sealless magnetic drive pump saved downtime and maintenance on a troublesome fume scrubber application.
The Problem
In this application, the company manufactures specialty chemical products in batches of up to 5,000 gallons using 37 percent hydrochloric acid (HCL) as a concentrated base reactant solution. Some of the reactions are endothermic, and some are exothermic.
When using the acid in a reactor, HCL fumes are often generated and emitted. The manufacturer had installed a fume scrubber using water as the scrubbing medium. The water is sprayed into a column packed with a plastic fibrous material.
A centrifugal blower takes emissions from the vessel and blows them through the column. As the HCL vapors meet the moisture from the water, they are absorbed and the clean air is released (see Figure 1).
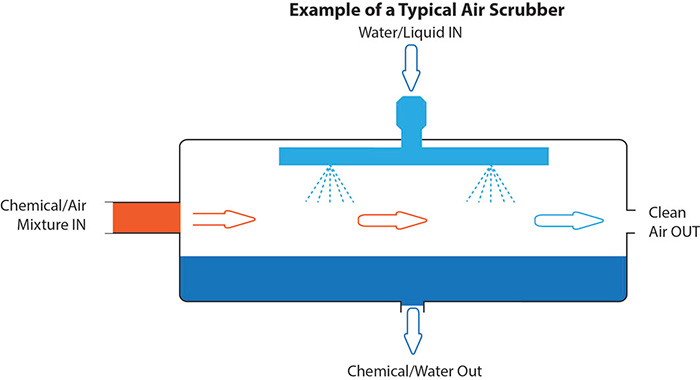
Figure 1. Example of a typical air scrubber (Images and graphics courtesy of IWAKI America)
Many companies neutralize the acidic scrubber contents and discharge them to waste treatment. In this particular case, the manufacturer needs to add water to the reaction process to control temperature. Adding the slightly acidic water from the scrubber is an ideal way to recycle what would normally be waste.
The concentrated solution of HCL and water is very corrosive. It is also a medium with air entrapped, sometimes causing cavitation in the pump. This combination plays havoc on traditional mechanical seals.
Mechanically sealed pumps typically carry a lower initial cost than sealless pumps. A pump's initial cost is typically less than 20 percent of its total life cycle cost (LCC). Factors such as energy and disposal costs are equal when considering LCC whether the pump is sealed or sealless. But factors such as maintenance, downtime and environmental costs can equal up to 50 percent of the LCC.
The most common reason a pump needs maintenance is a leaking mechanical seal. The three major reasons a mechanical seal will leak are open seal faces, heat generation and chemical attack.
Open Seal Face
The major contributor to a seal face opening is shaft movement, which can be either axial, radial or due to vibration. Axial movement is usually associated with varying pump operation during startup, shutdown or valves opening and closing. It can also be associated with temperature changes during process cycles or batches. Sealless pumps use high-strength magnets coupled with thrust surfaces designed for varying pump operation. They also use materials designed for varying temperatures.
Radial movement is associated with end play or shaft deflection when the pump runs past its best efficiency point. It is common when bearing frames wear and shaft deflection occurs. Sealless pumps are designed for full curve operation typically using dual thrust surfaces, and many of them are close-coupled, eliminating shaft-deflection risk. Vibration is usually found during cavitation periods when net positive suction head available is low or the pump is vortexing fluid from a supply tank. Sealless pumps typically using dual thrust surfaces are designed to handle moderate cavitation.
Heat Generation
Heat generation is often associated with dry-run conditions or prolonged cavitation. It can damage seal faces and elastomers, causing them to fail and degrade lower-grade seal materials. Many sealless pumps have dry-run sensors built into or around the pump to alert operators of such a condition. Some designs even have patented bearings that withstand dry-run conditions. Almost all sealless pumps have dual-thrust surfaces designed to handle moderate cavitation.
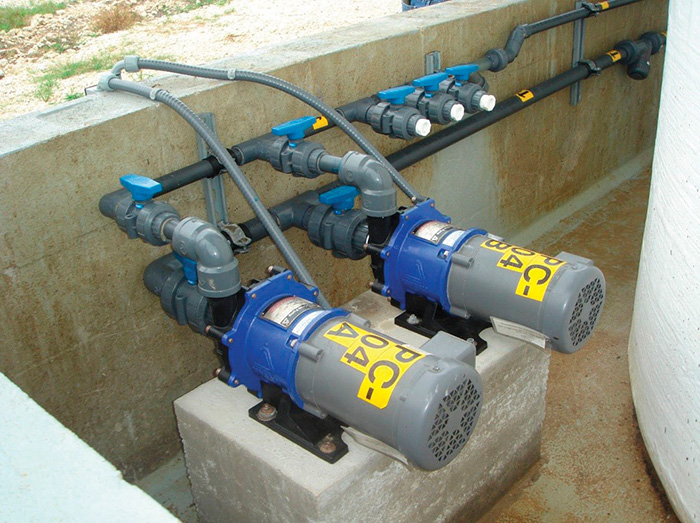
Image 1. Two pumps provide a run/spare scenario because a pump failure could place the company in violation of stringent emission standards.
Chemical Environment
Many fluids crystallize when exposed to air or heat from mechanical seals. Examples are caustics, seawater, brine, hydrocarbons and sugars. Sealless pumps have no contact with air. A chemical environment can promote corrosion, such as acids attacking carbon seal faces, chlorides attacking stainless steel faces and metal-finishing chemicals corroding metal bellows/set screws and plated seal faces. Sealless pumps come in high-alloy metallic and non-metallic materials for chemical applications.
Picking the Pump
This facility utilized magnetic drive pumps that feature a "no contact" bearing system ideal for cavitation situations. Proprietary high-strength magnets hold the rotating element in a neutral position that avoids contact with forward or rear thrust surfaces. The pump features ethylene tetrafluoroethylene, which provides strong corrosion resistance, and a carbon and ceramic bearing system. The carbon and ceramic with the magnets allowed the pump to run without fluid for brief periods.
This solved a troublesome and costly problem for this toll chemical manufacturer.
About the Author: Tom Marcone is the national sales manager for IWAKI America. He has more than 20 years of experience in chemical transfer and metering pump technologies. He can be reached at tmarcone@iwakiamerica.com or 508-474-2062. |